Fabric for emergencies
The specialist for medical textiles produces over 1.5 million first aid kits and boxes every year. These are not only used in an emergency in the event of a car accident, but also for first aid at work.
Almost everyone has the product in their car, but hardly anyone knows the company behind it: The company Hans Hepp GmbH & Co. KG in Hamburg has been producing first aid kits and bags for almost 90 years. They are mainly sold to the automotive industry, but also to the automotive accessories trade, drugstores and pharmacies. Many companies also use the first aid equipment from Hamburg in an emergency.
The bestseller is the classic first aid kit for cars in accordance with DIN 13164, of which HEPP produces over 1.5 million units per year! The family-run company also produces emergency kits especially for motorcyclists, cyclists and sailors. The secret of the Hamburg-based company’s success? ‘We deliver exactly what the customer needs at extremely short notice and with absolute reliability,’ explains Managing Partner Christian Beckmann. Because sterile products only have a shelf life of five years, the dressing material is not stored for long. And new vehicles cannot be delivered without a first aid kit: This is why HEPP delivers exactly as many sets as are needed on the delivery date of the cars.
This is possible because the company produces most of the bandage material itself. The backing material is produced on the automatic weaving machines in widths of six, eight or ten centimetres. Brief heating in the heat-setting machine makes the material elastic. Compresses are then applied to the carrier material by machine, the bandage packs are wrapped and packed in special paper. Finally, they are passed through a steam steriliser at around 130 degrees Celsius.
The plastic boxes are produced on an injection moulding machine
Even though the contents of most first aid kits are standardised, individuality is the key when it comes to packaging. Whether it’s a break-proof plastic box or a soft pocket cover, simple lettering or brightly coloured images, with a customer logo or neutral: ‘The packaging is produced in small batches exactly as the customer imagines it,’ says Beckmann during the visit to aktiv.
The Hamburg-based company also produces the first-aid boxes itself on a plastic injection moulding machine, including printing with the desired motifs. The bag covers, made of special material that is free of harmful substances and in some cases flame-retardant, are bought in.
Are the sealed seams really tight? Does the dressing pack remain sterile even in a hot summer car? ‘We have zero tolerance for errors,’ says quality inspector Tanja Hochsprung. Together with her colleague Svetlana Morasch, she carries out strict checks in the in-house laboratory.
The employees contribute to the safety of all of us
‘Our customers can therefore rest assured that the quality standards for medical products are strictly adhered to,’ says Hochsprung. If everything is in order, the first aid kits are assembled, packed and then delivered by hand by Magdalene Panusch and her colleagues.
Delays? There are none! ‘I can fully rely on my employees,’ says Beckmann. And many of the almost 40 employees have been with the company for decades. Probably also because they know: What they produce here makes an important contribution to the safety of us all. In cars, for sport and leisure – and also in many businesses.
Author: Silke Becker
Photos: aktiv/Jan Braukmeier
https://www.aktiv-online.de/news/erste-hilfe-verbandmaterial-von-hepp-aus-hamburg-faehrt-in-vielen-autos-mit-18723
Translated with DeepL.com (free version)
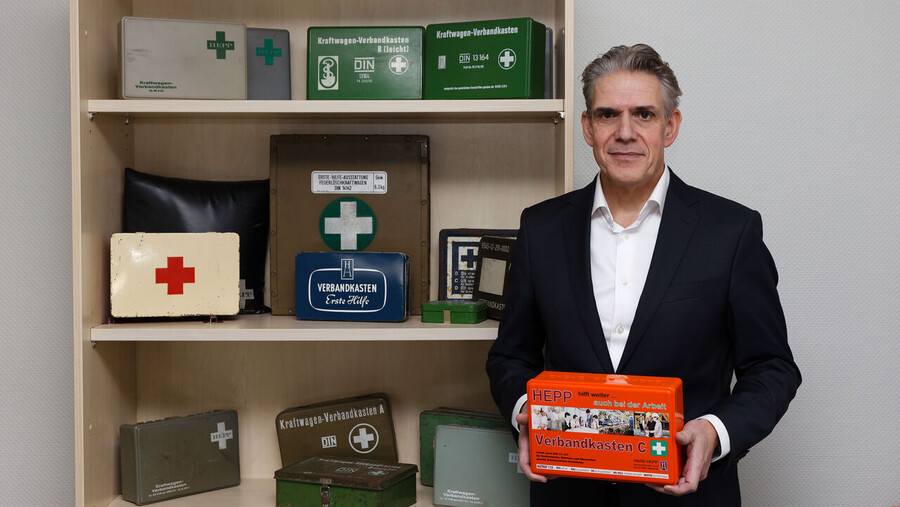